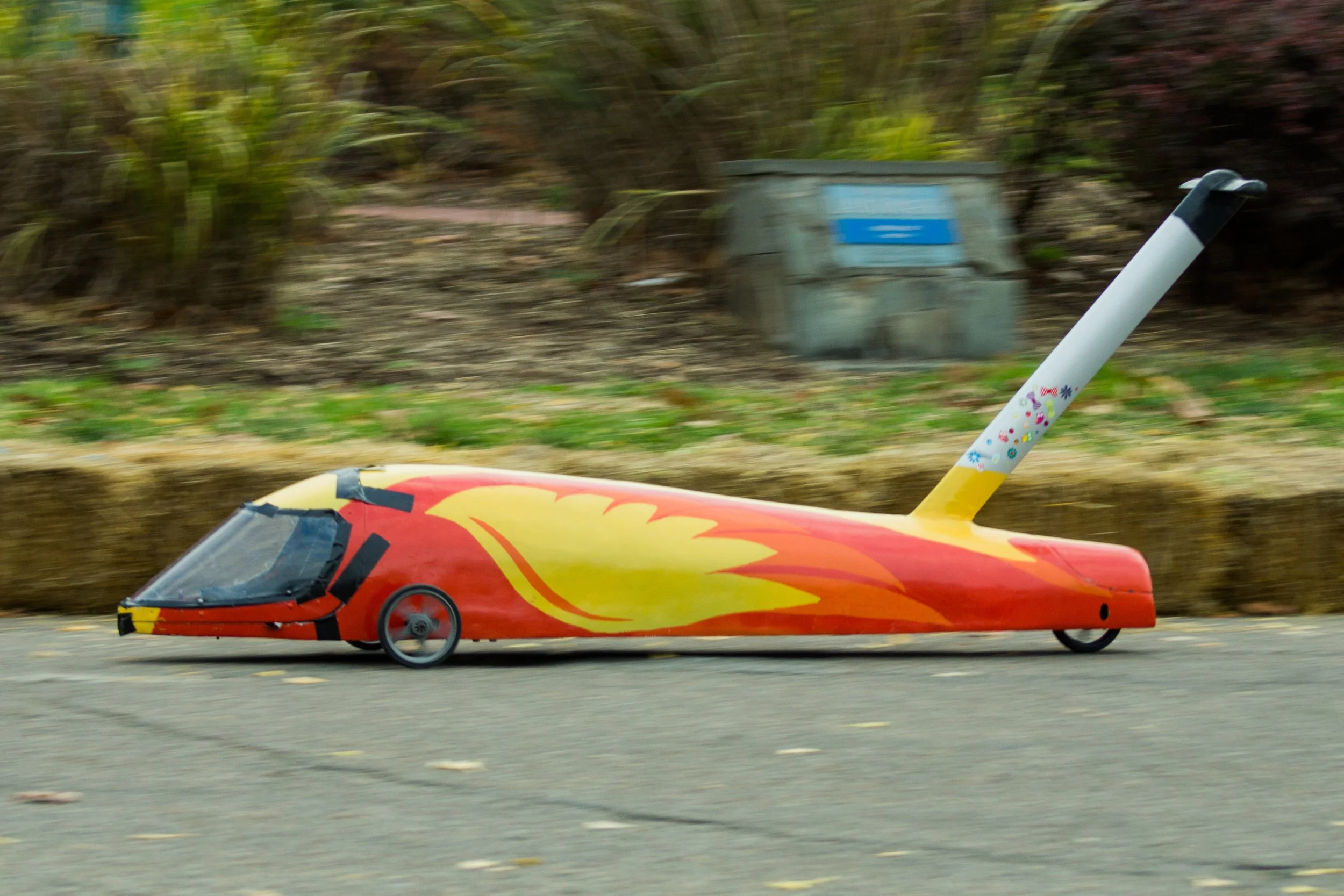
Phoenix Build - APEX Buggy
2011 - 2013
Sweepstakes (better known as "Buggy”) at Carnegie Mellon University is a human-powered vehicle competition. In this 100-year-old tradition, teams of five runners push an unpowered gravity vehicle (constructed entirely by students) containing a sixth teammate who drives the buggy. The race consists of two uphill segments where runners relay the buggy up the hills, and a free rolling downhill segment where the vehicle is controlled only by the driver and can reach speeds in excess of 40 miles per hour.
Race Day 2014 - Apex B Team
Despite this being a few years after the completion of the buggy construction project, this footage of an atypical ‘heat’ on Buggy race day is an excellent showcase of what the vehicle must be capable of once it has gone into service.
“Yes, there really is a person in there. No, they aren’t controlled by robots.”
-Answer to the question most frequently asked after seeing a buggy in action
In Fall 2012, I was elected co-chair of Apex Buggy alongside my colleague Connor Hayes. Our responsibilities expanded to include the fabrication of a new buggy, which was to be named "Phoenix". The documents below come from my design notes for that build process. Phoenix was completed in time to race during the Spring 2013 Sweepstakes event. Although not the fastest buggy, Phoenix is still racing to this day and can be seen out most weekends when teams practice. It can be spotted doing rounds around the race course located on Flagstaff Hill winding between Carnegie Mellon's campus and Phipps Conservatory.
This project would not have been possible without the entire Apex team. All members and advisors made significant contributions to the build.
A more detailed and comprehensive discussion about the Apex buggy team, the Pioneers buggy team, and the ‘open source buggy book’ can be found on the ‘Chute the Sh*t’ podcast produced by the CMU Buggy Alumni Association:
Season 4, Episode 1: Why Did Pioneers Die?: Inside the wild final days of Pioneer Buggy
Season 4, Episode 2: Open Door Policy: The Complete Story of Apex Buggy
Season 4, Episode 3: How to Build a Book About Building a Buggy: The Buggy Build Book
Buggies are often designed to fit one specific driver, their dimensions scaled to allow the driver to fit inside while also being as light as possible and using the least possible materials.
Phoenix's design was based on a buggy called "Chaos" operated by the Pioneers team. It was scaled to fit two different drivers taking measurements from each and creating a more versatile vehicle.
Buggies are typically constructed with light weight composites like fiberglass, kevlar, or carbon fiber. These fabrics are layered into a mold to form the structure of the vehicle. For this buggy a ‘male mold’ was created so that it could be wrapped in carbon fiber. These pictures show the construction process that was used for the ‘Phoenix Build’ mold which was built out of insulation foam glued together, coated in automotive body filler and sanded smooth. This type of mold is destructively extracted from the inside of the buggy after the layup process is complete leaving space on the inside hollow. The surface finish of the mold was critical as it would determine the surface against which the driver would operate the vehicle.
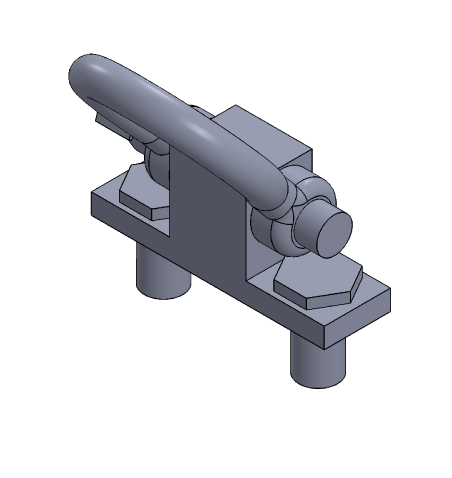
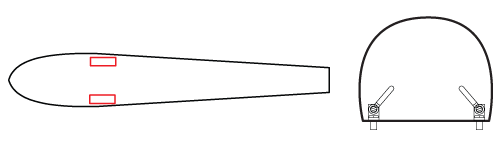
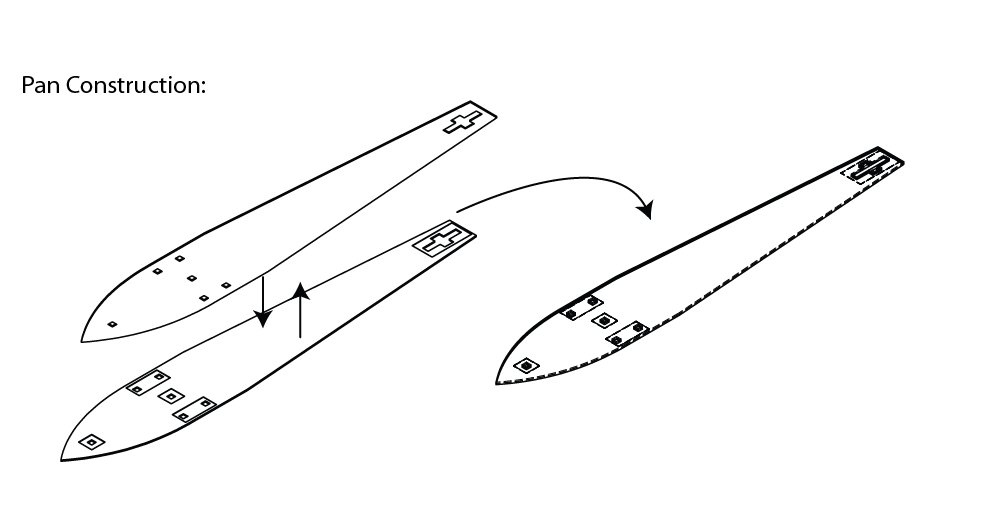

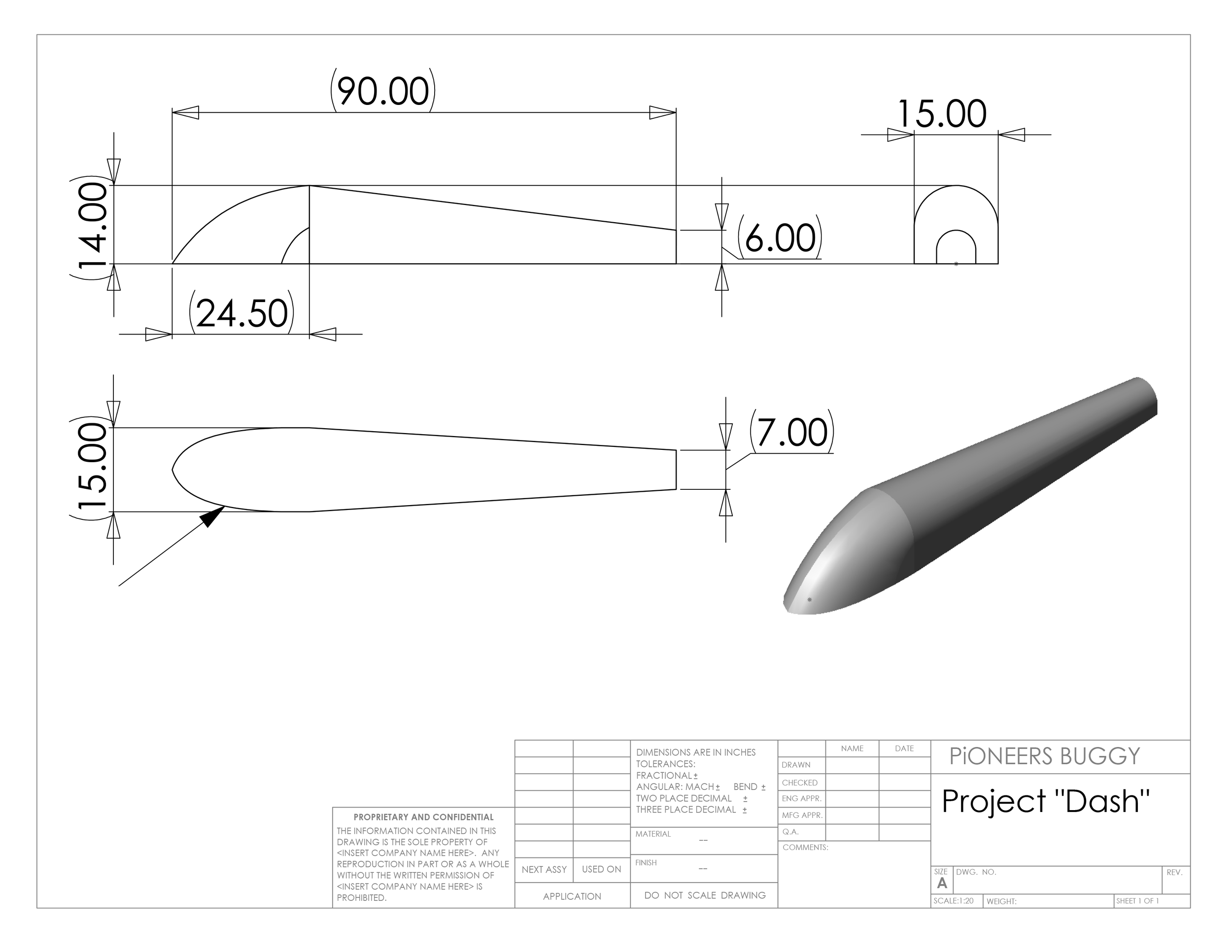
After designs were discussed with the team and drawings were created in CAD fabrication quickly commenced.
Functional parts including ‘hard points’ embedded in the shell were machined in-house by students on a manual vertical mill and a bench-top metal lathe. Many variations were designed and attempted before eventually outsourcing final designs due to time constraints. Pictured here are prototypes being aligned and tests being performed on potential materials.
Coating the mold in woven carbon fiber cloth that has been saturated with resin is a process known as “wraps” in the buggy community. Wraps are performed in relatively quick succession usually about ~8 hours after the previous step to ensure that the epoxy will be not fully cured aka ‘green’ which promotes adhesion between layers.
Once the mold has been fully covered by carbon fiber it is placed into an air-tight bag and subjected to a vacuum pump in order to apply even pressure across the entirety of the irregularly shaped mold. The buggy would be constructed out of a series of wraps, repeated layers of carbon fiber, a nomex honeycomb for added rigidity and weight reduction, a marine-grade ‘endgrain’ balsa wood bottom and more layers of carbon fiber.
A video was created by the on-campus film making club CMU TV that documented this process and collected interviews with some of the team members.
This was unheard of at the time. Because it was possible for teams to gain a competitive advantage though technological breakthroughs or refinement in fabrication processes the sport of Buggy was typically cloaked in secrecy.
Unfortunately this made it especially difficult for new student organizations such as Apex to fabricate their own vehicles. The team decided to do everything in their power to open-source the process, tools, techniques, failures, and methods so that information would be available to new buggy teams in the future.
These principals and the desire to expand the sport would eventually lead to the ‘How to Build a Buggy’ Book created by the heroic efforts of Connor Hayes and Diya Nuxoll
After the first two layers of wraps the base plate is added to the bottom of the mold creating the ‘pan and shell’ construction technique. The balsa wood base plate is also a deviation from typical buggy construction which favors more lightweight materials. In this case the buggy was being designed for longevity and the end-grain balsa wood typically used in marine construction had orders of magnitude more compressive strength then other materials in consideration.
After the final wraps are complete the mold is kept under vacuum pressure until the epoxy fully cures. The final product is a very dense 'torpedo-like’ solid object that will need to be cut open. Once it is accessible the mold will be destructively removed creating a hollow tube.
Any areas that cured with wrinkled fibers and critical areas around the hatches, and edges of the shell were reinforced with a mixture of fiberglass beads and epoxy resin to provide better abrasion and chipping resistance. Some cosmetic body filler was also added before the painting process.
With the shell complete the vehicle now needs all the mechanical components, such as wheels, brakes, steering systems, wind shield, safety harness attachment points and the ‘push bar’ which allows the runners to move the buggy along the course. These components were all entirely fabricated by students on-site and required a number of iterations before a solution was created with enough rigidity and reliability to be entered into the races.
After the vehicle was completed and finally named “Phoenix” it was tested by “Sweepstakes” the governing body of the sport of buggy to ensure safety and braking capability.
The vehicle was then cycled through the course up to a dozen times every weekend until race day, gradually increasing speed until the driver (Mallory Hayase - pictured throughout) reached a minimum number of practice heats
The buggy was eventually given a coat of paint for it’s 2014 raceday premiere. But future teams of students would greatly improve on the initial paint job in the following years. Phoenix would wear many outfits over it’s lifetime….
My favorite paint job was done by the artist ‘Berrymeat’ aka Rika or ‘Vix N dwnq’ and is featured in the header image for this page.
The race record for this buggy can be found here:
https://cmubuggy.org/history/buggy/phoenix13
It has been more then a decade since we put the finishing touches on the buggy and its still going strong! I say we had succeeded in building a durable and reliable vehicle capable of being modified and iterated on by teams of students for years to come.
In closing I want to once again state that This project would not have been possible without the entire Apex team. Both the 2012/2013 members and all those who came after as well as everyone who offered their time and expertise and support to insure the success of this new team and their first buggy.